激光焊接是利用激光束优异的方向性和高功率密度等特性进行工作,通过光学系统将激光束聚焦在很小的区域内,在极短的时间内使被焊处形成一个能量高度集中的热源区,从而使被焊物熔化并形成牢固的焊点和焊缝。作为一种高精密的焊接方式,其极为灵活、精确和高效,能够满足动力电池生产过程中的性能要求,是动力电池制造过程中的首选。
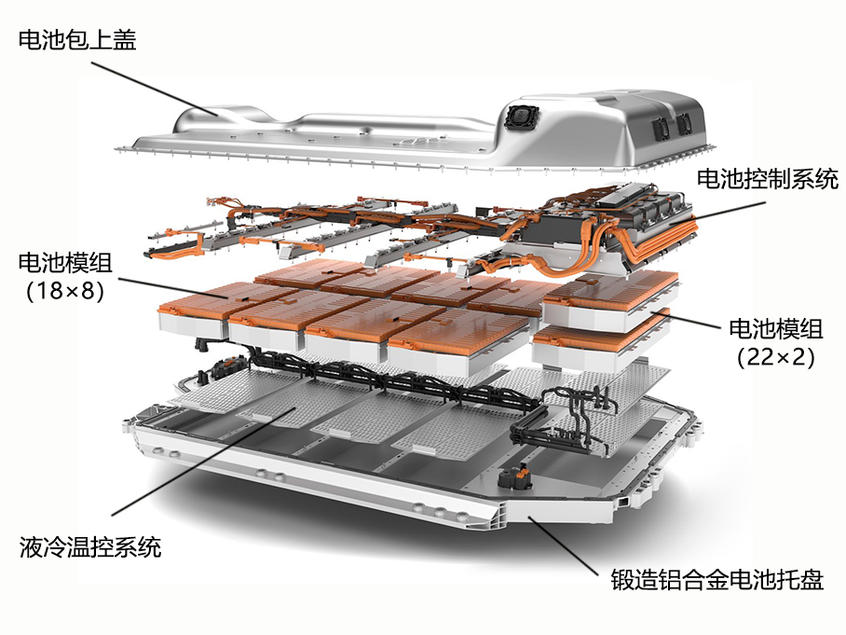
在动力电池的生产中使用激光焊接的环节在电芯组装环节与电池PACK环节。
1、电芯组装工段-中段:激光焊接工艺应用于壳体、顶盖、密封钉、极耳等焊接环节。
电芯组装工段具体包括电芯的卷绕、叠片、极耳焊接、电芯入壳、外壳顶盖焊、注液、注液口封装等。电芯是动力电池的最小单位,电芯的质量决定了电池模组的性能进而影响整个动力电池系统的可靠性。相比传统氩弧焊,电阻焊的方式,激光焊接具有显著优势:
- 热影响区窄,焊接变形小,特别适合于微型件的焊接;
- 通过光导纤维引导或棱镜偏转,可远距离施焊;
- 具有极高的能量密度;
- 不需要真空防护和x射线防护,也不受磁场影响。
2、后处理工段-后段:激光智能化焊接系统替代传统手工装配方式应用于模组PACK
后处理工段具体环节包括化成分容,测试分档、PACK模组,主要设备包括化成机、分容检测装置、过程仓储物流自动化,PACK自动化设备。其中,激光自动化系统普遍应用于模组PACK组装产线,进行电池PACK模组时的连接片焊接。
此外,激光也可以用于模组后的盖板上的防爆阀焊接等。防爆阀通常是由激光焊接成一定形状的两个铝质金属片,其上设计有凹槽,当电池压力过高时破裂泄压。由于防爆阀与盖板的配合间隙小,很难准确放到位,因而对激光焊接工艺要求极为严格,要求焊缝密封,严格控制热输入量,保证焊缝的破坏压力值稳定在一定范围内,否则会对电池的安全性造成较大影响。防爆阀通常采用拼接焊,复合焊。随着激光焊接工艺不断精进,激光焊接渗透率有望提升。
作为行业内领先的细分领域智能化激光焊接解决方案服务商,新耐视自主研发的两款焊接利器—NewScan-3D振镜激光飞行焊接头和NewFA3钎熔焊送丝焊接头可分别在动力电池制造过程中不同的环节应用。
NewScan-3D振镜激光飞行焊接头
应用场景:防爆阀、极柱、密封钉、转接片、Busbar等

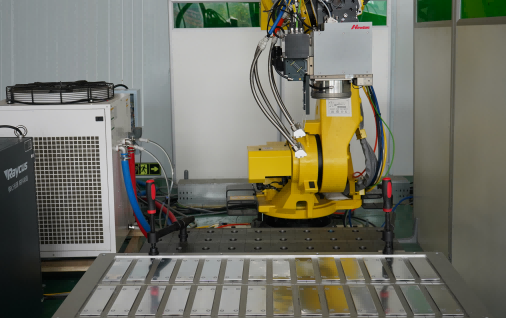
NewFA3钎熔焊送丝焊接头
应用场景:电池包、端侧板,电池托盘、水冷板等部位焊接

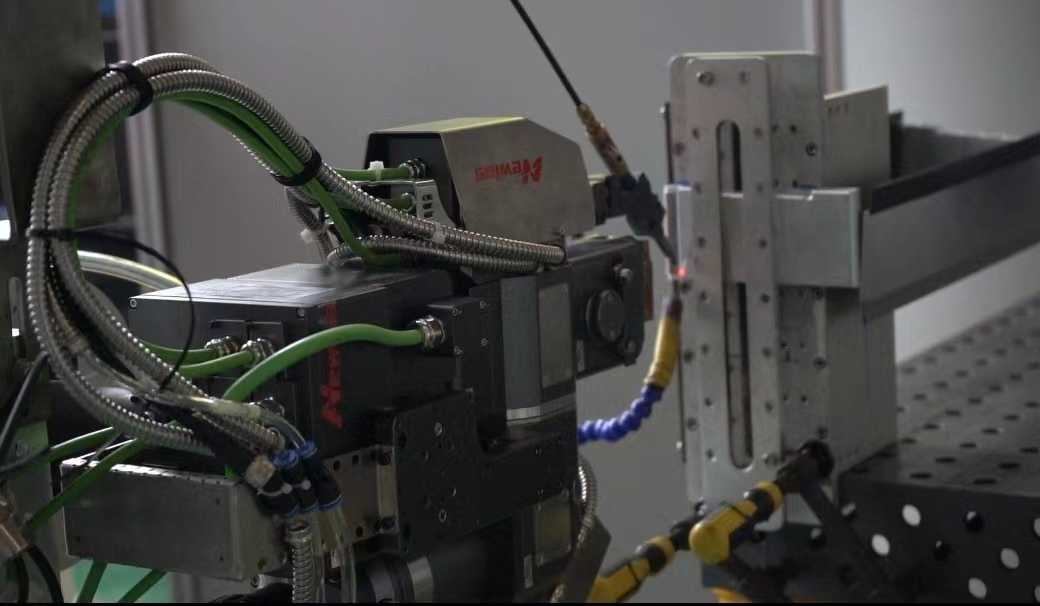
武汉新耐视智能科技有限责任公司成立于2017年12月,深耕智能化高功率激光精密焊接技术,是一家以“让焊接更简单”为理念,以解决企业激光焊接产线“卡脖子”问题,实现激光制造装备数字化、智能化为目标的高科技公司。
公司具备从激光焊接工艺、“焊前-焊中-焊后”全流程检测与控制、关键部件到整机系统研发一体化的能力,公司基于自主设计的国产化高功率智能激光焊接设备,可提供工艺前期测试与打样,降低客户现场调试时间与项目实施风险,新耐视以创新为驱动,具备丰富的行业经验,致力于为主机厂和集成商提供全面的新能源汽车、动力电池行业激光焊接解决方案。