激光钎焊具有高效、精确、无污染等优点,可以提高车身的强度和刚性,同时降低车身的重量。其中,车顶激光钎焊长度最长、质量要求最高、控制难度最大,其焊接质量的稳定性和可靠性对于保证车身的安全至关重要。下文将介绍新耐视NewLBO 3D焊缝寻位与质量检测系统在汽车车顶焊接中的应用。
一、激光三角测量法原理
NewLBO 3D视觉检测采用激光三角测量法原理对工件表面进行高度测量,基于线结构光的三维视觉测量,通过附加一个运动方向的位移,来获取工件表面的高度信息,进而实现高精度的尺寸测量和缺陷检测。
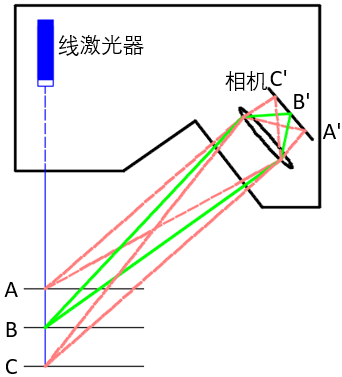
二、NewLBO 3D焊缝寻位与质量检测系统介绍
NewLBO 3D焊缝寻位与质量检测系统主要包含3D相机、机器人和焊缝检测软件处理系统。3D相机用于采集被检焊缝表面形貌三维数据,在机器人移动过程中,焊缝检测软件快速分析高密度点云数据进而检测焊缝质量,实现焊缝长度、宽度、深度/高度测量,可检测气孔、漏焊、塌陷、焊瘤、飞溅等缺陷,同时完成与外界信号的交互与反馈、数据参数加载与保存等,实时界面,可人工查看扫描形貌和分析结果。
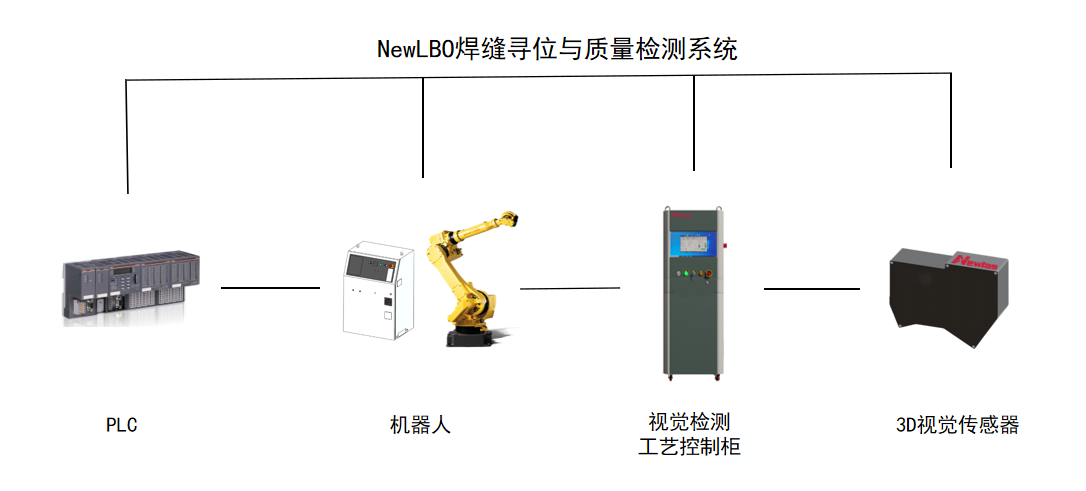
系统优势
- 高效可靠的缺陷识别和检测
- 自定义焊缝几何尺寸测量
- 焊缝位置变动检测
- 在线/离线分析,结果可视化
- 2D/3D图形化再现焊缝细节
三、产品应用
- 2D缺陷识别
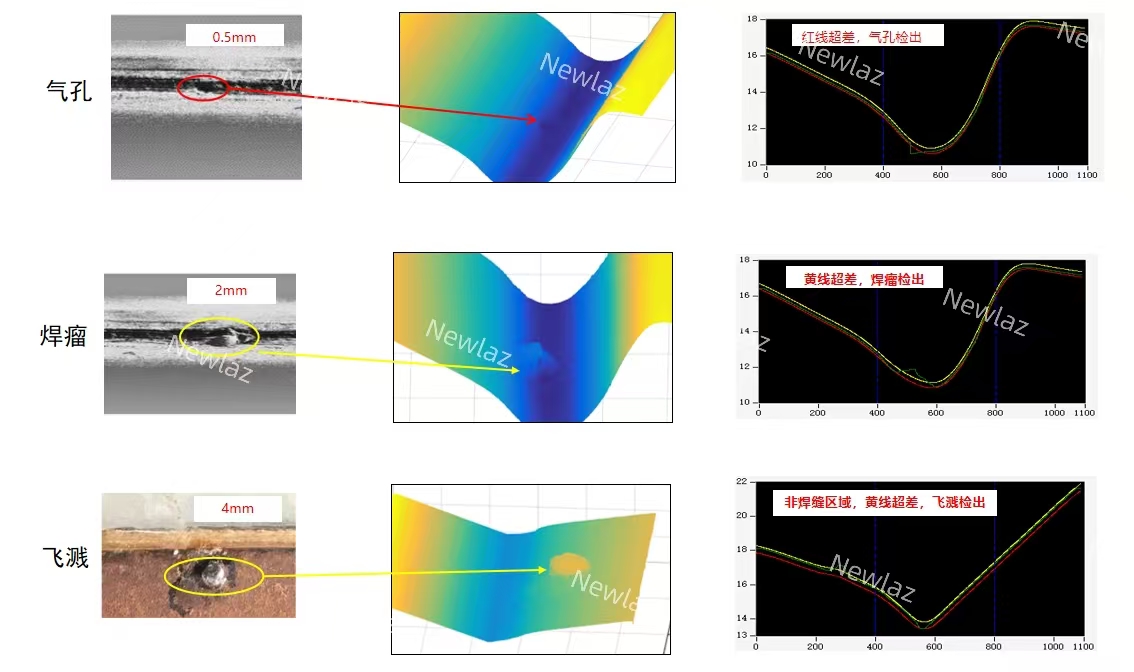
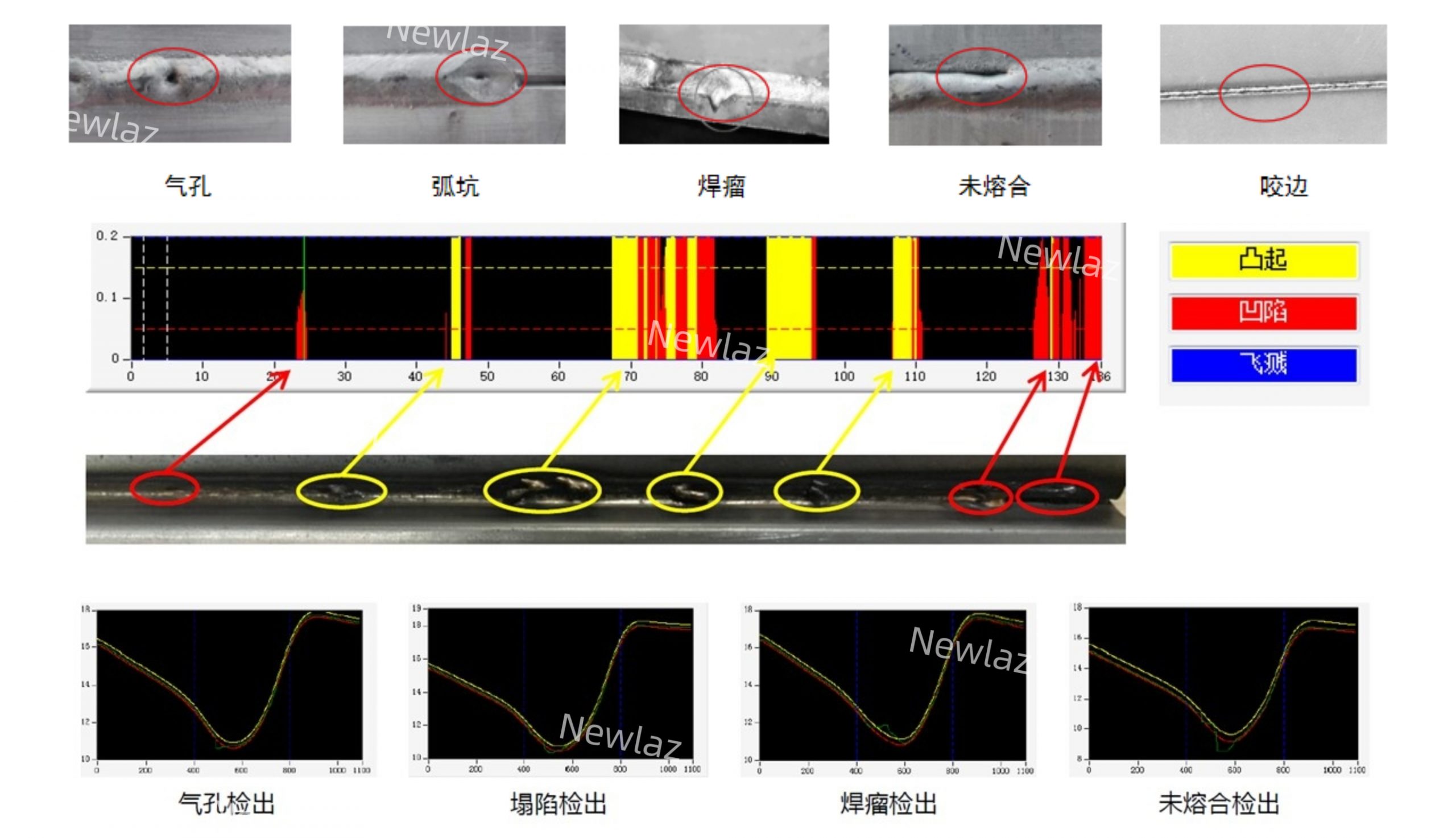
- 3D缺陷检测
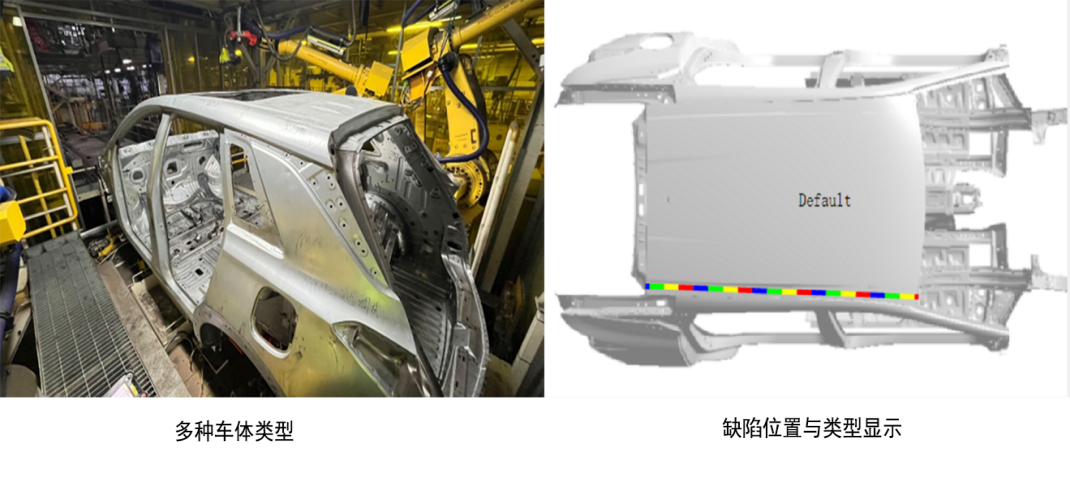
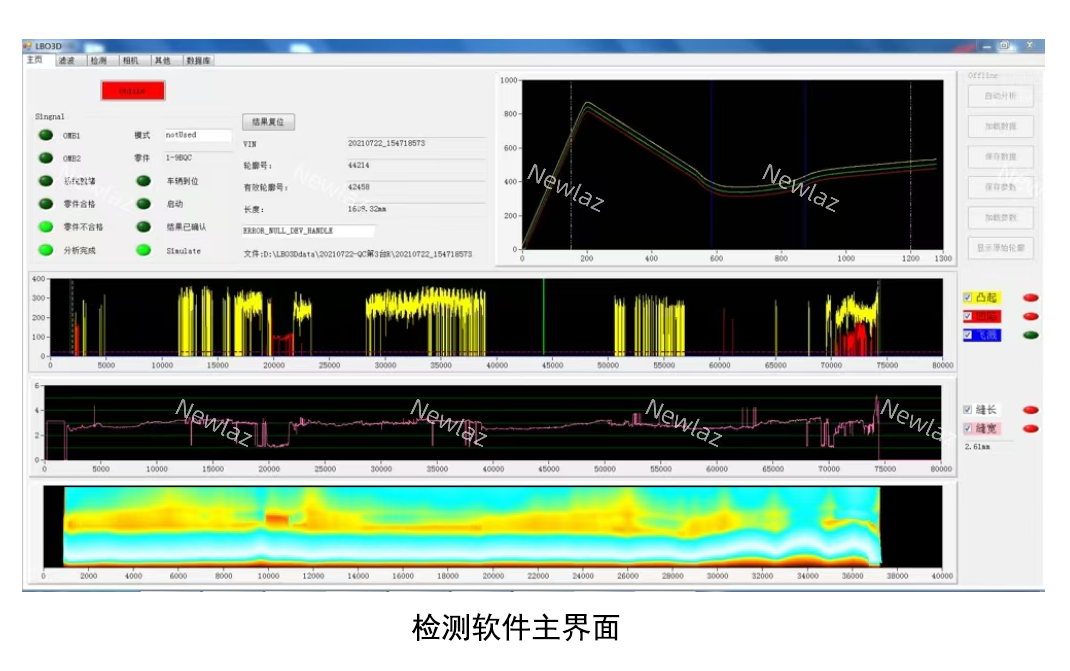
- 现场检测实况
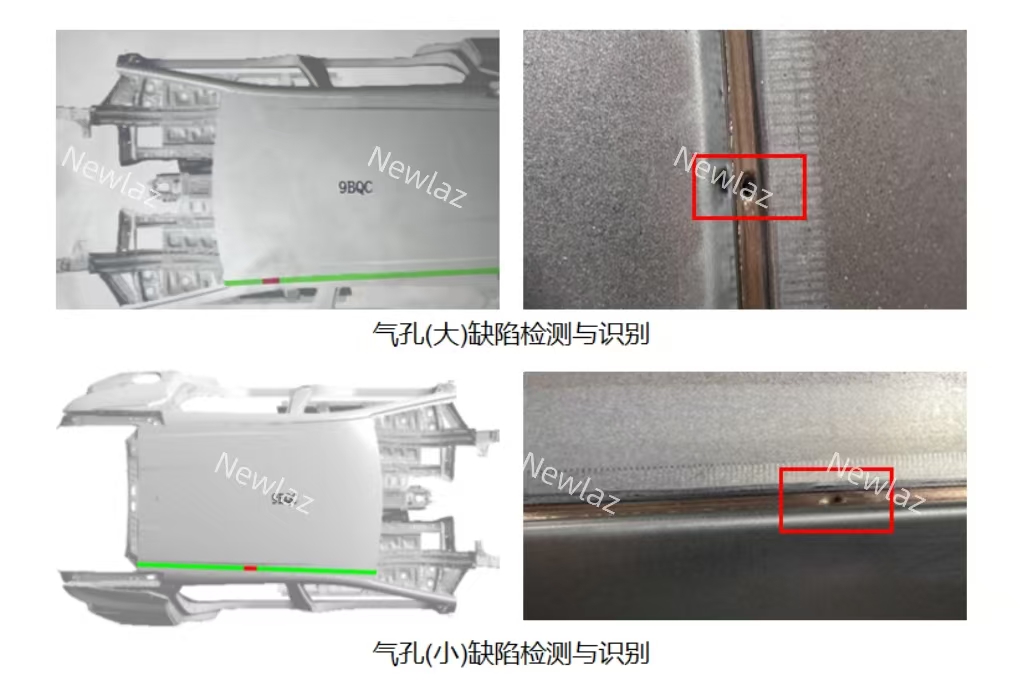
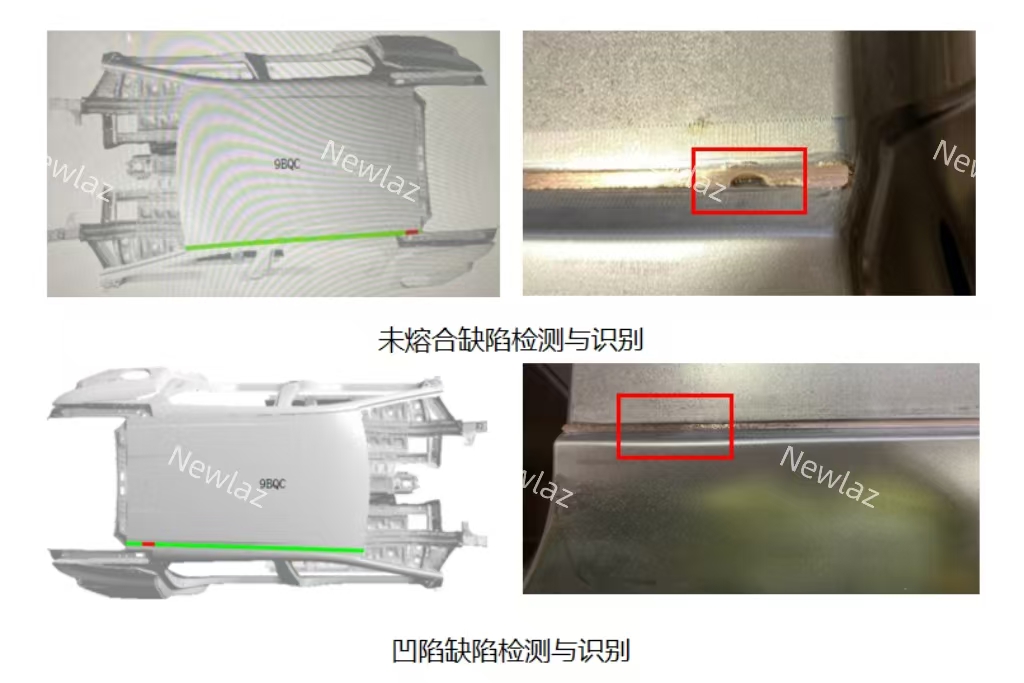
汽车顶盖侧围制造采用激光钎焊不仅拥有传统点焊、MIG/MAG焊难以比拟的焊缝强度和良好的焊缝外观,而且焊接效率高,已成为汽车顶盖制造的标准工艺。为了便于生产管理者随时了解焊接情况,实时进行质量控制,新耐视研发了NewLBO 3D焊缝寻位与质量检测系统,可以在线检测焊接过程中焊缝存在的缺陷,显著降低时间成本,让生产更加高效轻松,实现自动化、柔性化、智能化的汽车制造。