对于功能强大的电机尤其针对新能源电动汽车应用使用矩形截面的铜线(即扁铜线)生产定子已成为普遍现象。激光技术已被证明是可以用于定子生产的关键工艺去漆与焊接的高质量生产方式。去漆工艺采用脉冲激光去除所有常见的绝缘材料。扁铜线焊接工艺中,基于图像定位的激光高速振镜焊接已在速度和安装空间使用方面被证明是一种高效的方案。
由于电动汽车需求的增长,电机制造商在为高产能、高质量焊接寻求更有生产力的工艺,更高程度自动化的实现是高产能需求的根本保证。因此,扁线型定子在很大程度上占了上风:制造商开始使用压缩空气将矩形铜线(因其形状而称为“扁铜线”)插入整个定子槽中,而不是像以前那样在单个定子槽周围缠绕圆铜线。扁铜线矩形横截面的典型边缘长度在2至4 mm之间。该过程实现了更高的生产速度,并且可以轻松实现自动化。由于扁铜线比圆导线更硬,扁铜线在电机中的对准可以被更好地控制。填充系数越大,热负载容量越高,电机功率也越大。铜线涂有绝缘层,需要在两端局部消融(扁铜线去漆)以实现接触,在这里使用脉冲激光加工。与机械加工(如刨削和铣削)相比,激光加工的生产率提高了80%。
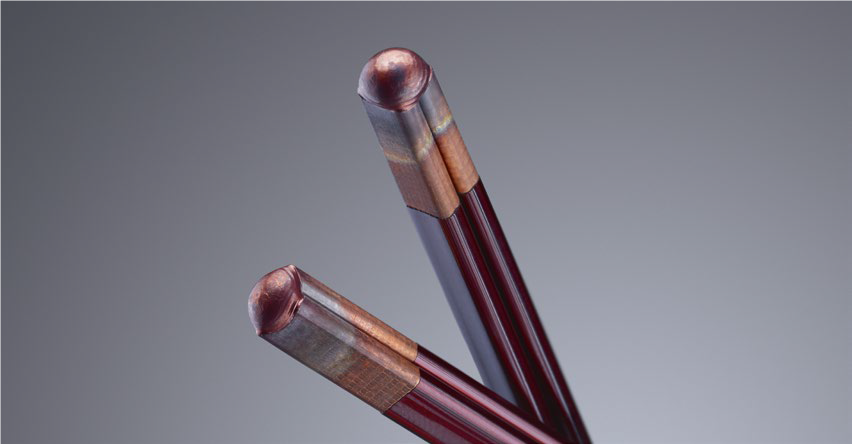
扁铜线嵌入槽中后,定子顶部和底部的突出端将被夹具(“扭头”)拧在一起或固定到位,然后进行焊接。然而两端并不总是理想地相互对齐。如果使用自动识别定位焊接,集成在激光光学系统中的基于图像识别的传感器系统有助于实现可靠和可再现的结果,从而使电机获得可能的最高电流。
一、扁铜线去漆
扁铜线常见绝缘层:
•Polyamide-imides (PAI)
•Polyether ether ketone (PEEK)
•Polyamide-imides with polyimide foil (PAI+FEP)
过去,PAI 涂层在行业内几乎是最为常见的,但近期 PEEK 和 PAI+FEP 涂层的应用有稳定增长的趋势。尽管 PAI 仍是迄今为止最广泛应用的涂层材料。
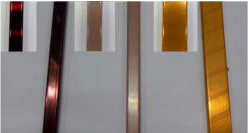
1. 消融工艺
使用脉冲激光消融工艺将铜表面的绝缘涂层清洁、高效地剥离。激光聚焦到绝缘层中,在纳秒时间内输入能量并将其消融。PEEK 对激光的吸收率较高;对于 PAI 和 PAI+FEP,建议使用激光脉冲预先处理以增加吸收率。
铜或会由于激光消融的部分热影响而变色。但是变色并不影响后续工艺,因为铜的结构并未发生改变。在绝缘涂层与铜线的边界处有可能产生毛刺,在后续焊接工艺中,极端情况下毛刺部分有粘在周围的部件或夹具上的风险。如需要,可选择使用飞秒脉冲进行二次加工,将极大优化毛刺和变色现象。
在高效的消融过程中,可以使用 TruMicro 7070 和 TruMicro 7060 短脉冲激光器。使用 TruMark 7000 和 5000 系列激光打标系统可实现良好的去漆效果。使用焦距 160mm 的聚焦镜以尽可能提高消融效率; 搭配合理的激光器数量配置 (见下文),可以进一步优化效率。根据工艺参数的不同,激光消融工艺后的铜线表面会存在微结构。这种影响可以通过增加频率或调整聚焦位置被最小化。该工艺分两步进行首先是剥离绝缘层,然后是清洗铜线表面(生产中使用两套不同的激光参数)。例如 TruMark 7050 去漆时的频率为 55kHz。第一次应以大约 1m/s 左右的高速完成,然后以 600mm/s 的速度重复三次。对于清洗,单次建议使用 255kHz 和 3000mm/s 的速度。在涂层厚度不均匀的情况下,将工艺参数对准较厚的一侧是很重要的。根据扁铜线类型的不同,可以实现 0.3 到 3cm 以 2/s 的加工速度。
PEEK 的消融过程:可以看到过程窗口边界的碳化。用飞秒激光器返工可以提高质量。
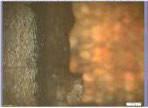
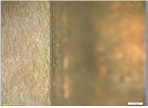
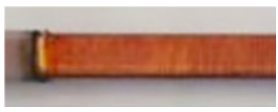
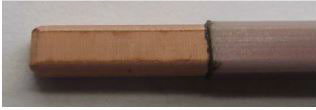
2. 工艺方法
使用激光可以将分离好的单个扁铜线进行去漆,也可以基于整条铜线进行去漆。例如可使用连续进料方式进行在线工艺,这种方式在扁铜线生产中应用最为广泛。根据切线机的进料速度,可编程聚焦光学振镜(PFOs)必须进行不同的配置,以保持去漆位置位于 PFOs 工作区域。以下为三种可使用的配置策略建议:
a. 从四个方向以 90° 角度进行加工,基于 TruMicro 7060 实现。使用四个焦距 160mm 的 PFO 振镜及 460μm 的方形光纤组合。每两个 PFO 的组合使用 50:50 的能量分光。TruMicro 可配置 4 个出光口和 2 个分光模块。在完成第一步扁铜线的两个相对面去漆后,铜线剥漆位置从出光口 1 和 2 移动至出光口 3 和 4。此方案的最大单次去漆长度是 56mm。
b. 从三个方向以 120° 角度进行加工。此种配置方法较为经济,去漆效率中等,一般选择 TruMark 7000 系列并配置长焦深。对于特定的扁铜线种类,也可以用 TruMicro 7060 来实现, 聚焦镜焦距一般选择 160mm。如选用TruMark 系列,由于单台设备功率较低,每台设备都仅配置一个出光口及单独振镜,即需要三台设备实现工艺;如使用 TruMicro 系列,凭借其较高的功率优势可以通过分光方式,实现一个光束源搭载三个 PFO 振镜的形式。
c. 从两个方向以小于 60° 角度进行加工。这种配置方式仅推荐使用 TruMicro 7070,此种去漆方式存在一定的侧边绝缘涂层残留风险。
取决于绝缘层的材质,使用 TruMicro 系列,PAI 涂层扁铜线可以达到最高 13cm2/s (平均 7cm2/s) 的去漆效率。使用 TruMark 系统,PAI 涂层扁铜线可以达到 4cm2/s 的去漆效率。在去漆工艺中,激光工艺比机械加工快 40% 到 80%。
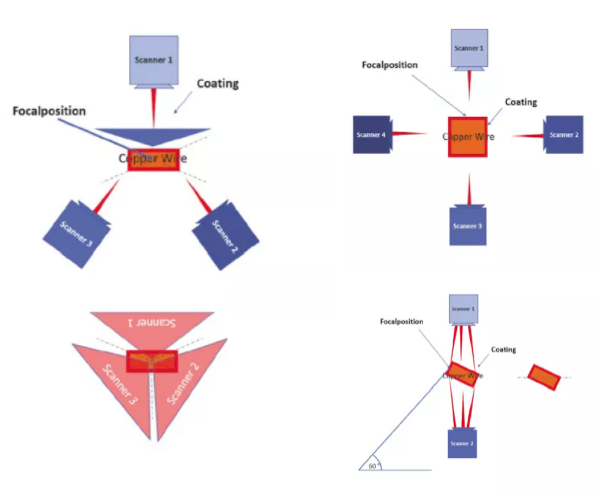
右上:在铜线的四个表面以90°进行加工
右下:在铜线的两个表面以小于60°进行加工,这种方法只有 矩形线才有可能,焦点必须被设置在铜线中心
二、扁铜线的焊接
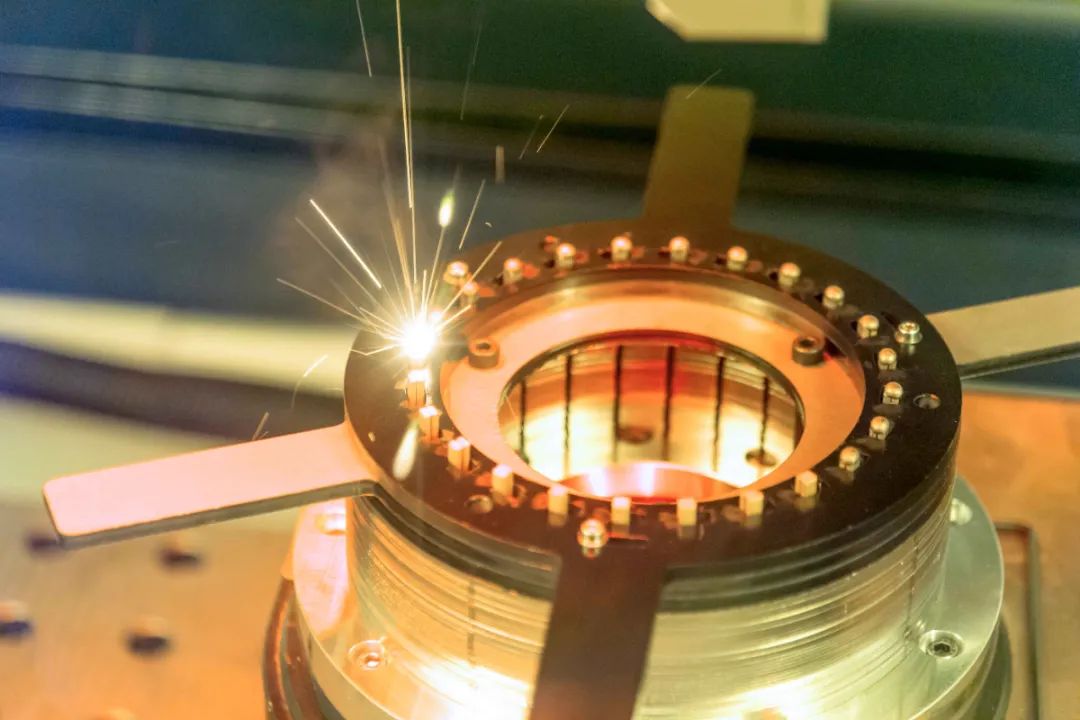
在插 Pin 制程之后,定子上的扁铜线凸起端必须被一对一对地焊接在一起以实现最佳的物理接触。在焊接准备过程中,切线机将扁铜线切割分离,在铜线端口形成剪切后的光滑表面,接着被扭到一起或者被固定到位。这里存在相当大的位置公差,扁铜线不可能总是被完美地互相对齐。涉及到高度偏移和间隙宽度的公差可能会对焊接过程产生负面影响,因为公差过大将减小有效连接面。另一方面,焊接工艺对焊缝公差的要求非常严格。这个挑战必须在焊接过程中解决。
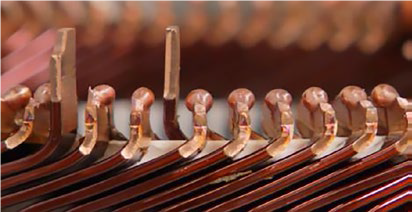
在焊接准备中,我们推荐用吸尘设备清洁扁铜线上可能的污染物。可最大程度的避免定子和夹具上的一些焊接缺陷和飞溅。
扁铜线焊接应用解决方案可选择 TruDisk 3001 至 8001 激光器系列与 TruLaser Cell 3000 自动化平台。激光器波长为 1030 nm,最大功率 6kW。
基于以上方案可实现高速、高品质焊接(单个扁铜线焊点 t ≤ 0.4 s,取决于扁铜线的尺寸)。
由于需焊接的每对扁铜线位置、方向、对齐程度并非总是符合标准焊接参数所接受的公差,我们使用 PFO 高速振镜,并通过图像捕捉系统(VisionLine)进行定位。基于摄像头的传感器系统将预先检测每一对铜线的位置和方向,并与振镜自动实时校准,从而使扁铜线中的小间隙和定位偏差可以通过补正来继续焊接工艺。
激光、光学模块和检测系统高度集成,基本实现自动运行,必要时也可单独实现功能。基本上,一个这样的标准化系统即可满足生产。
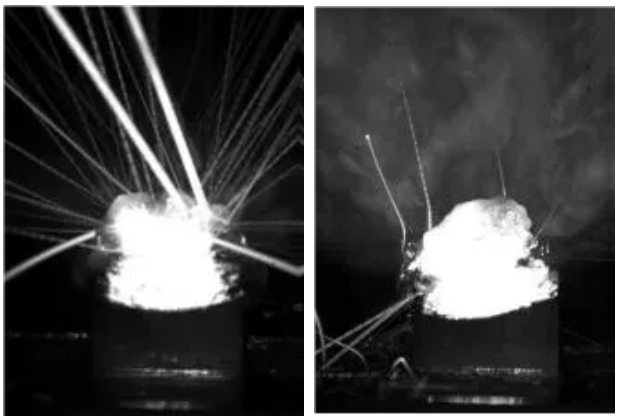
右图:通过优化光束使飞溅大幅减少
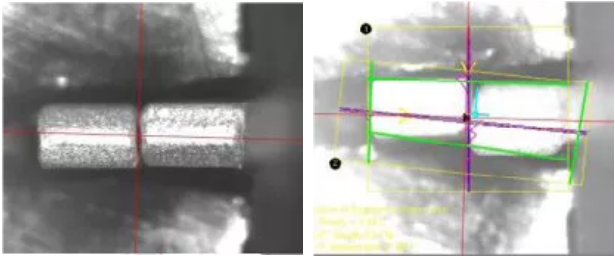
我们使用摆动焊接以覆盖较大的间隙。为了优化扁铜线焊接工艺,得到更好的焊点,需要对激光焊接光束的摆动路径进行优化。在这里,如果扁铜线在其短边连接,特别推荐线型摆动焊接轨迹;另一方面,如果要在长边连接,则要选择圆形或椭圆形摆动焊接轨迹。通过这种工艺,我们实现了高速焊接并最小化飞溅和气孔的形成,实现的焊缝具有很高的抗拉强度与良好的熔深,可使扁铜线获得最佳导电性。此外,激光焊点的悬垂几乎为零的特性给铁芯凹槽和扁铜线位置更加靠近提供可能。这意味着当电机的安装空间固定时,可实现更紧凑的电机设计。
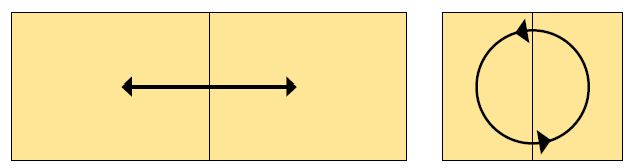
右图:两个扁铜线长连接的圆形摆动焊接几何示意图
在扁铜线去漆工艺中,脉冲激光消融是非常经济可靠的工艺方案。我们可提供三种不同的去漆方案以满足不同需求,客户可根据自身实际情况选用不同的工艺方案及光学配置,与机械工艺相比,去漆效率最高可以提升80%。在扁铜线焊接工艺中,搭载 PFO 高速振镜与图像捕捉系统 (VisionLine) 的 TruDisk 3001、5000、6001 或 8001 激光器系列可实现高效、高质量焊接。碟片激光器、高速光学振镜和图像捕捉系统的结合同时满足了电机扁铜线焊接的高质量(低飞溅和气孔)与高产能需求。此外,光学振镜也为目标元件多样的焊缝外形提供了极为灵活的解决方案。