目前,汽车顶盖与侧围主流连接方式有电阻点焊和激光钎焊两种。电阻点焊技术成熟,应用广泛,顶盖连接应用最多的就是这种方式。
激光钎焊也称激光填丝钎焊,是在电弧钎焊的基础上发展起来的一种钎焊技术,具有外观好、速度快、结构简单等优点。
本文主要介绍顶盖采用电阻点焊和激光钎焊的优势、劣势,为产品设计开发提供参考。
1. 工作原理
电阻点焊是通过点焊电极对被焊工件施加并保持一定的压力,使工件稳定接触,然后使利用电流通过焊件,使接触表面产生热量,温度升高,融化接触点,局部形成焊点(如图 1所示)。
激光钎焊是利用激光光束作为热源,聚焦后的光束照射在填充的焊丝表面,焊丝被光束能量加热融化形成高温液态金属,液态金属浸润到被焊零件连接处,在界面层生成均匀的固溶体和共晶组织,使之与工件形成良好的冶金结合(如图2所示)。
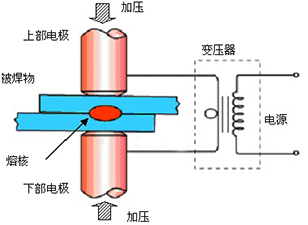
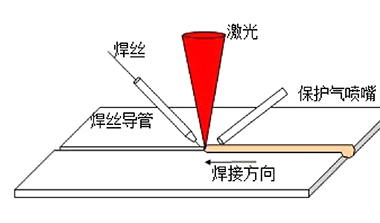
2. 优劣对比
2.1 连接结构
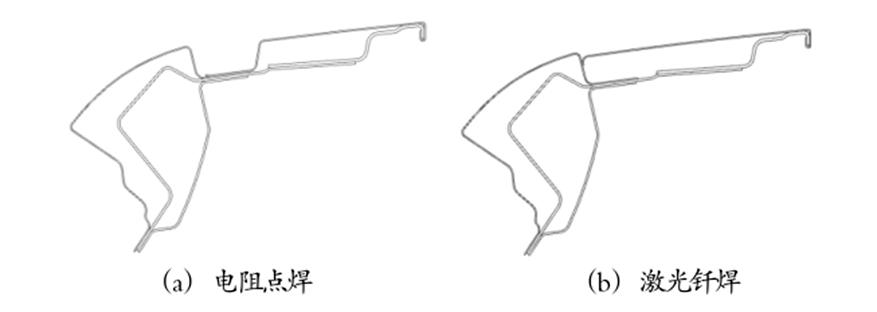
1)焊接刚度
由上图可知,在全景天窗的焊接中,电阻点焊的侧围腔体与顶盖腔体被隔开,顶盖中部的刚度差。
激光钎焊的两个腔体紧密相邻,顶盖中部的刚度好且性能更优。
2)灵活性
点焊技术由于其焊枪本身体积较大,电极头工作需要一定的机械运动轨迹,在结构设计中需要做结构特征或减小结构尺寸对焊枪进行避让,所以结构设计上存在诸多限制。
激光钎焊是单面焊接,肉眼可见的地方均可以焊接,极大地增加了结构设计的灵活性,可以获得更优的结构。
3)焊接工艺
电阻点焊顶盖边缘采用台阶结构,而激光钎焊则为翻边结构且翻边角度为负角,因此在顶盖冲压工艺中,激光钎焊所用的顶盖必须增加一个翻边工序才能实现此结构,综合顶盖整体工艺设计可能会导致增加一套冲压模具。
4)生产规划
在非全景天窗车型中,传统电阻点焊工艺的顶梁是与顶盖焊接成为一个整体再上总拼线,顶梁的焊接集成到分拼工位上,未占用总拼的场地和布置。
采用激光钎焊工艺后,顶梁无法与顶盖焊接,顶梁必须先在总拼线上与侧围焊接后,再将顶盖上件并进行激光焊接,这时总拼线上工艺过程增多,占用了紧张的总拼线资源,对生产线布置要求较高,对场地的需求也高。
2.2 外观
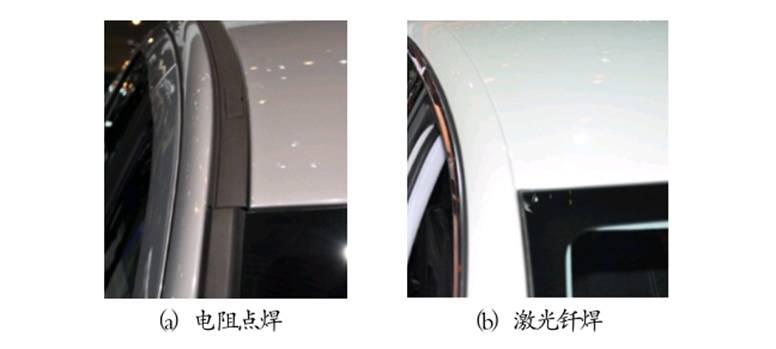
电阻点焊结构有一凹槽(即流水槽),流水槽内有电阻点焊,由于点焊外观一般不为客户接受,因此需要在流水槽安装一个饰条,以便遮挡点焊(如图4(a)),但这种方式会导致顶盖与侧围连接处特征线较多,还要考虑饰条与前挡风玻璃的匹配程度,设计复杂,外观较差。
在客户使用一段时间后,饰条唇边、零件凹槽处会积聚灰尘、落叶、杂物等,唇边、凹槽特征狭小,其中的污垢难以简单清除,进而会使车辆外观显得脏、旧。
激光钎焊则不存在上述问题,首先,顶盖与侧围直接搭接,无饰条,没有多余的零件,仅搭接处的一条特征线(如图4(b)),并且此特征线会由前挡风玻璃的下端一直延伸到顶盖末端(即尾门处),整体结构简单、自然、过渡平顺,外观极佳。
激光钎焊处外表面平整,不会藏污纳垢,即使落有一些灰尘、杂物,只需简单擦拭即可清除,方便客户进行日常清理,也会让车辆显得光鲜、干净。因此,从产品设计外观到日常使用的外观,使用激光钎焊的车辆外观均远远优于电阻点焊。
2.3 焊接速度
电阻点焊为间歇焊接,焊接速度约1.9 m/min(焊点间距按80 mm,2.5 s焊1个焊点)。
激光钎焊速度为4.2m/min,相比而言,激光钎焊速度更快,生产工时更短,利于加快生产节拍。
2.4 焊接材料
当前,电阻点焊只能进行钢与钢的焊接,铝与铝的电阻点焊技术尚不成熟,在行业内仅有个别车企使用,铝与铝电阻点焊技术有带极点焊和铝点焊等,目前仅有“通用”“特斯拉”使用铝点焊。因此,当前电阻点焊只能用于传统的钢车身。
激光钎焊既可以连接钢与钢,还能连接铝与铝,既能用于传统钢车身,还能用于全铝车身,因此采用激光钎焊技术对向全铝车身发展的车企具备一定的兼容性。同时,电阻点焊焊接镀锌板较为困难,对工艺要求较高,而激光钎焊对镀锌板适应良好。
2.5 单车成本
1)电阻点焊需要增加车顶饰条,在涂装车间还需涂密封胶。激光钎焊无饰条,但需要消耗钎焊丝,综合来看,采用激光钎焊,单车成本更低。
2)电阻点焊与激光钎焊在能耗成本、日常运行成本上也有差异,但总成本小。电阻点焊焊接顶盖,耗电约0.48 kW/台车,使用自来水冷却,无保护气体,激光钎焊耗电约0.04 kW/台车(4 kW×36 s/3 600×2道),使用过滤后的纯净水,采用氩气作为保护气体。
3)电阻点焊会消耗电极帽,激光钎焊导电嘴不时需要更换。
3. 技术风险
电阻点焊发展时间长,技术成熟,主机厂完全具备相关能力。激光钎焊作为近几十年发展起来的技术,对主机厂的制造水平要求较高。
激光钎焊对零件搭接精度要求极高,一般要求搭接间隙为0.1~0.35 mm,间隙过大会导致焊钎熔料下沉,甚至掉落(如图5所示)。由于激光钎焊搭接精度远超电阻点焊的要求,因此原有方式已无法满足激光钎焊的要求。行业内通常是在焊接时增加预紧夹具,把顶盖压向侧围,避免搭接离空,例如某公司采用一种琴键式夹板夹具固定顶盖(如图6所示)。
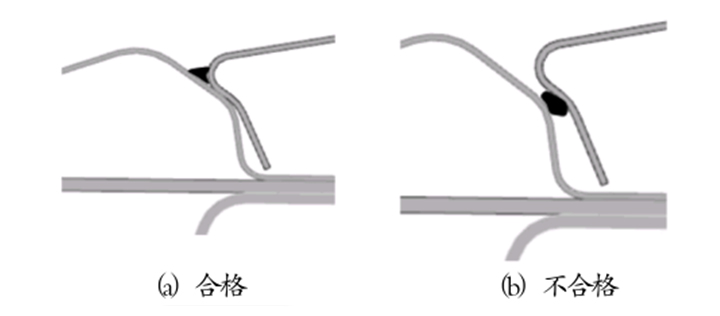
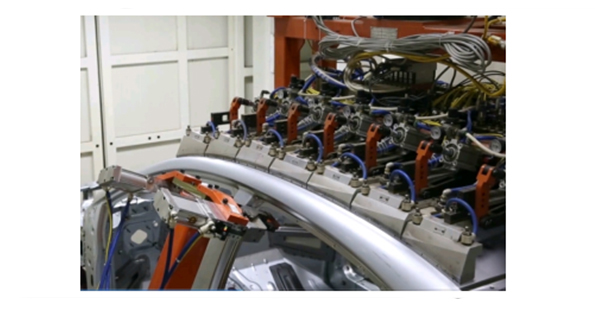
4. 总结
相比电阻点焊方式,顶盖与侧围的连接采用激光钎焊方式,顶盖刚度高、外观好,生产速度快,同时取消了车顶饰条和密封胶,单车成本降低。但是,激光钎焊固定投资大,生产柔性差,对零件搭接精度高,生产上必须保证顶盖与侧围间隙。
电阻点焊方式是车身连接传统的生产技术,顶盖采用此技术与已有的生产系统兼容性好,固定投资小,对生产精度要求低,但结构设计复杂,整车成本较高。
文章来源:《企业科技与发展》期刊